Filling & Capping Monoblock for Skin Care Lotion
Home » Case studies » Applications » Hair & Body Care » Filling & Capping Monoblock for Skin Care Lotion
Project Description
This filler-capper Monoblock was developed for a leading Canadian brand specialized in Beauty & Personal Care Products.
This Monoblock system was designed to fill highly viscous skin lotion products and cap various types of dosing pumps at a rate of 100 units per minute.
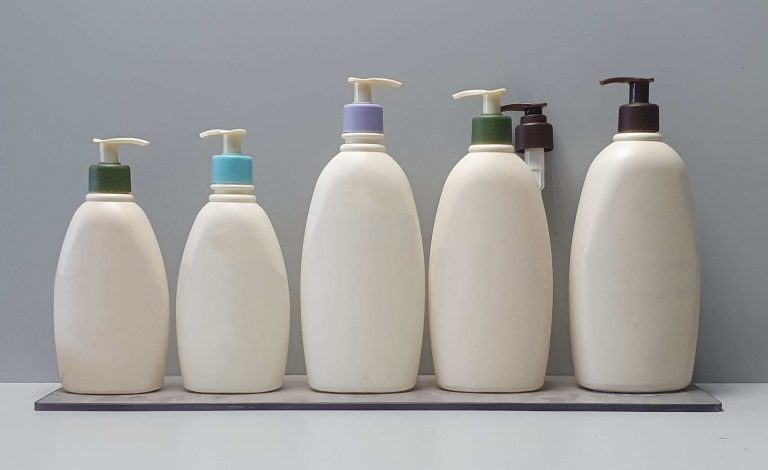
The Challenge
The task involved addressing key needs of our client including consistent and accurate filling of skincare lotion into oval-shaped HDPE containers ranging from 12oz to 24oz.
The complexity lay not only in handling the products with high viscosity across diverse container sizes but also in accommodating the unique oval shape and using six different dosing pump types within the same machine.
Furthermore, another key objective of the project was to optimize changeover processes and improve cleaning procedures given the physical characteristics of the skincare lotions.
How did Mengibar solve it?
Mengibar came up with a state-of-the-art solution that integrates viscous filling heads, ensuring a uniform product flow. This innovation not only significantly reduces filling time but also effectively mitigates the risk of splashing, enhancing precision and minimizing product waste.
Mengibar has also delivered the pioneering Predictive Tendency Analysis, which rapidly identifies and rectifies any potential flow fluctuations and maintains an uninterrupted filling process.
Mengibar effectively solved the challenge of accommodating different types of oval containers and dosing pump caps.
The machine allows quick and simple adjustments to suit various container types. Switching between pump types is also smooth, requiring no tools. This applies to both the automatic feeder sorter and the capper machine.
Moreover, the system features a stationary 360° Clean-In-Place/Sterilize-In-Place (CIP/SIP) Drain Pan, providing quick cleaning and changeover times. The Monoblock system has a hygienic design, incorporating non-contact nozzles that eliminate any potential risk of cross-contamination.
Eliminating mesh and flow restrictors from the nozzles reduces maintenance efforts, directly contributing to increased productivity.