Rotary Capping Machinery
Home » Capping Machines » Rotary Capping Machinery
The Complete Capping Solution
Mengibar’s Rotary Capping Machinery can work either with Trigger Sprayers, Dosing Pumps, Caps with dip tube or Regular Caps with just a quick change over. Like the rest of Mengibar Rotary Cappers, these machines can be equipped with the most advanced quality control systems such as Vision Systems, Cameras, Servomotors for torque control or cap Orientation, Electronic ServoCam, etc.
Mengibar has the ability to find the right solution, for even the most difficult and imposible to solve applications in the market, in a simple and useful way and with a reasonable cost.
Rotary Capping Machines are manufactured as stand-alone units or integrated with other Mengibar equipments in a Rotary Monoblock.
Pump Cappers: Versatile Capping Solution with One Machine
Trigger Pumps and Dosing Pumps are essential closures in various household applications, including detergents, window cleaners, degreasers, and liquid soaps. Mengibar, with over 30 years of experience, has been at the forefront of manufacturing Trigger Pump and Dosing Pump Cappers, as well as Monoblocks.
Our advanced technology allows Mengibar’s Cappers to handle a wide range of cap types with a single machine, offering unparalleled versatility and efficiency. This includes trigger pumps, dosing pumps, caps with dip tubes, and regular caps. Our machines are designed to meet the highest standards of precision and reliability, ensuring that each closure is securely and accurately applied, regardless of the cap type.
Innovative Technology and Benefits
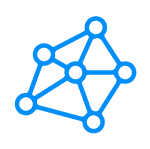
Versatility
Any type of closures (Trigger Pumps Dosing Pumps, Caps with dip tube, Snap-on Oriented Caps, Screw-on Caps, Plugs, Fine mist sprayers, spouts, etc). One single Capping Machine can be fed with different Cap Sorters for different applications.
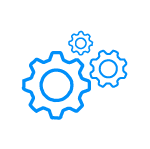
Complete Solution
One single solution provider guarantees the efficiency of the whole sorting and capping operation. Mengibar manufactures not only the Capping Machine but also the Automated Sorters, Conveyors, etc.
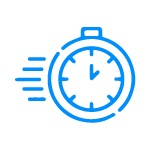
Reduced footprint
Mengibar Plug & Play and Poka-Yoke concept design for detachable color coded parts (no human errors on installation). Automated adjustments recipe driven. Minimum time required on changeover.
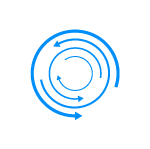
Torque control
For screw-on closures based on Dynamic Torque Principle by means of individual servomotors in each capping station. New torque values are easily selected as part of the recipe menu for each SKU. A pop-up alert warns in case that any closure doesn’t meet the preset values and finally that bottle will be diverted from the main discharge conveyor.
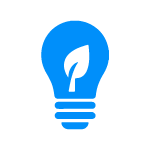
Real Time Production Management
Regenerative Energy Supply. In the event of an emergency stop (power failure, air failure, safety microswitches activated, emergency push button, etc.) the kinetic energy of the machine decelerating is used to keep the ServoCam modules in motion until the machine is stopped.
Innovative Technology and Benefits
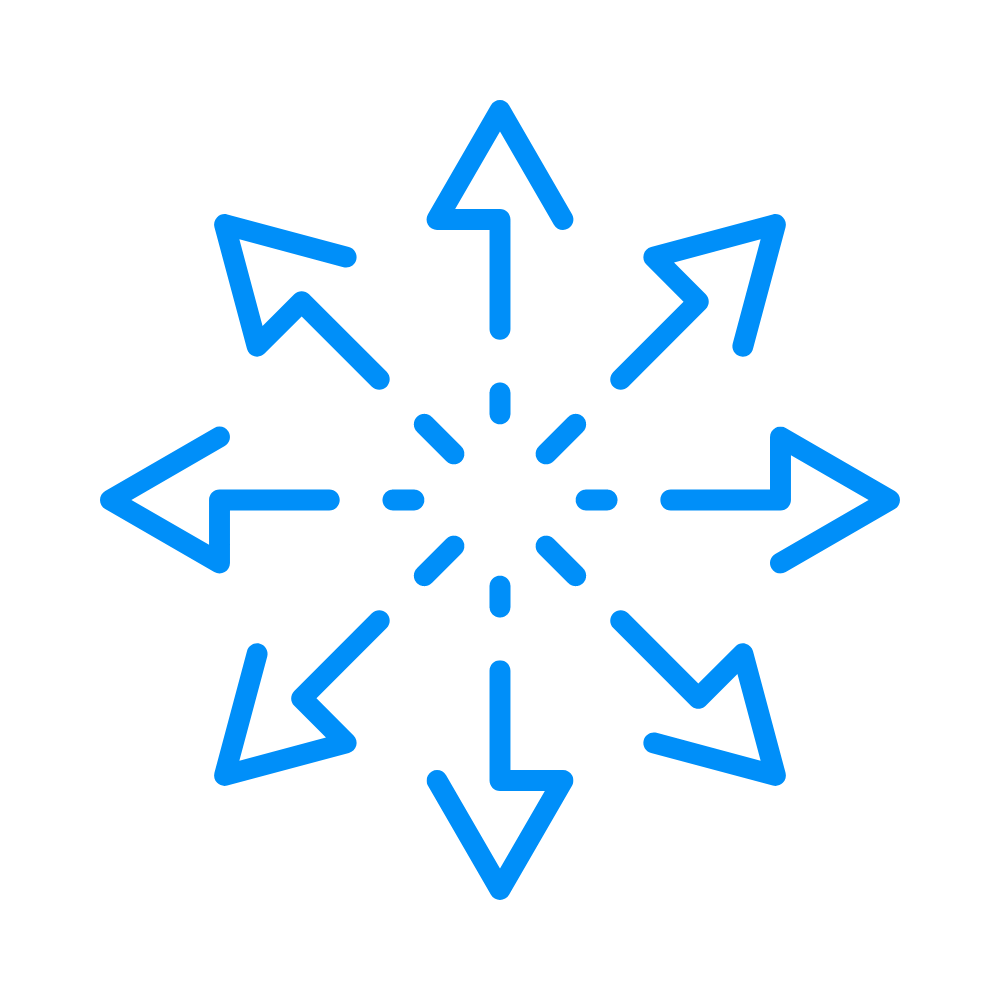
Versatility
Cap multiple types of closures with a single machine, reducing the need for multiple pieces of equipment and streamlining production processes.
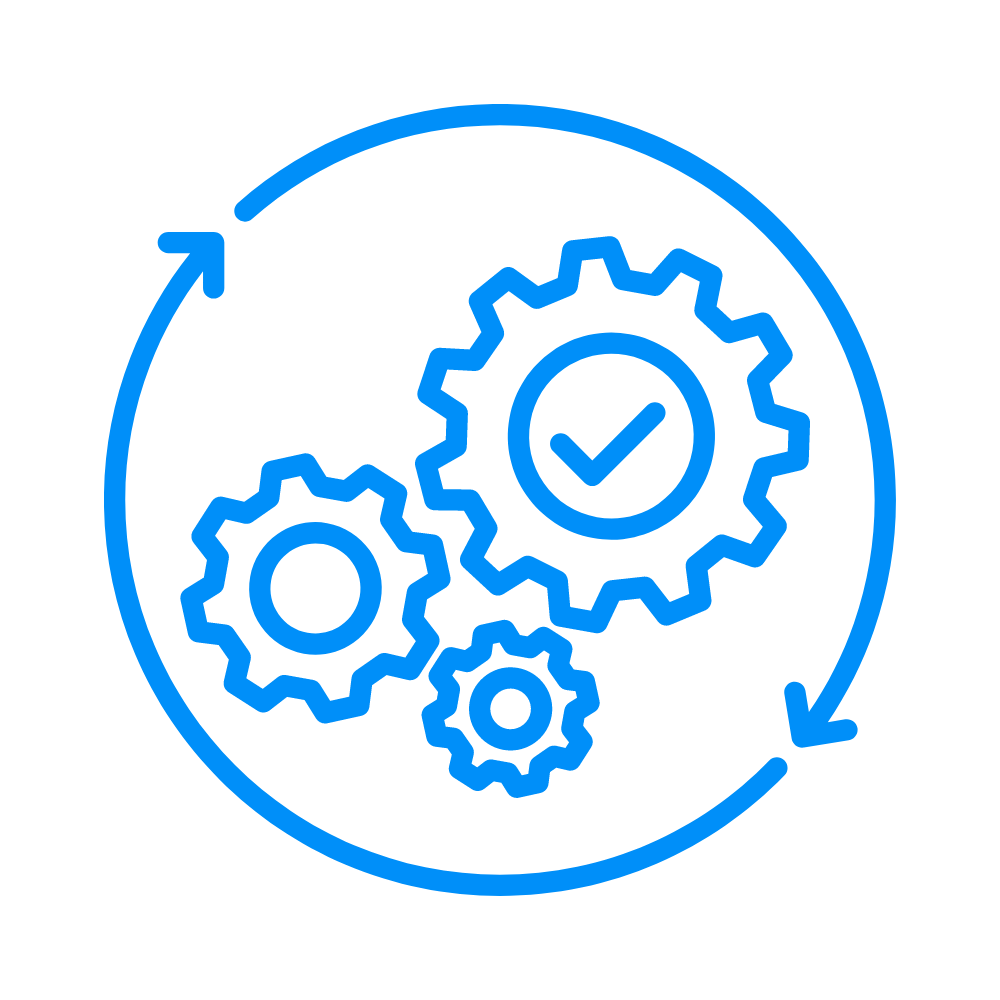
Efficiency
Our state-of-the-art machinery ensures fast and accurate capping, enhancing productivity while maintaining product integrity.
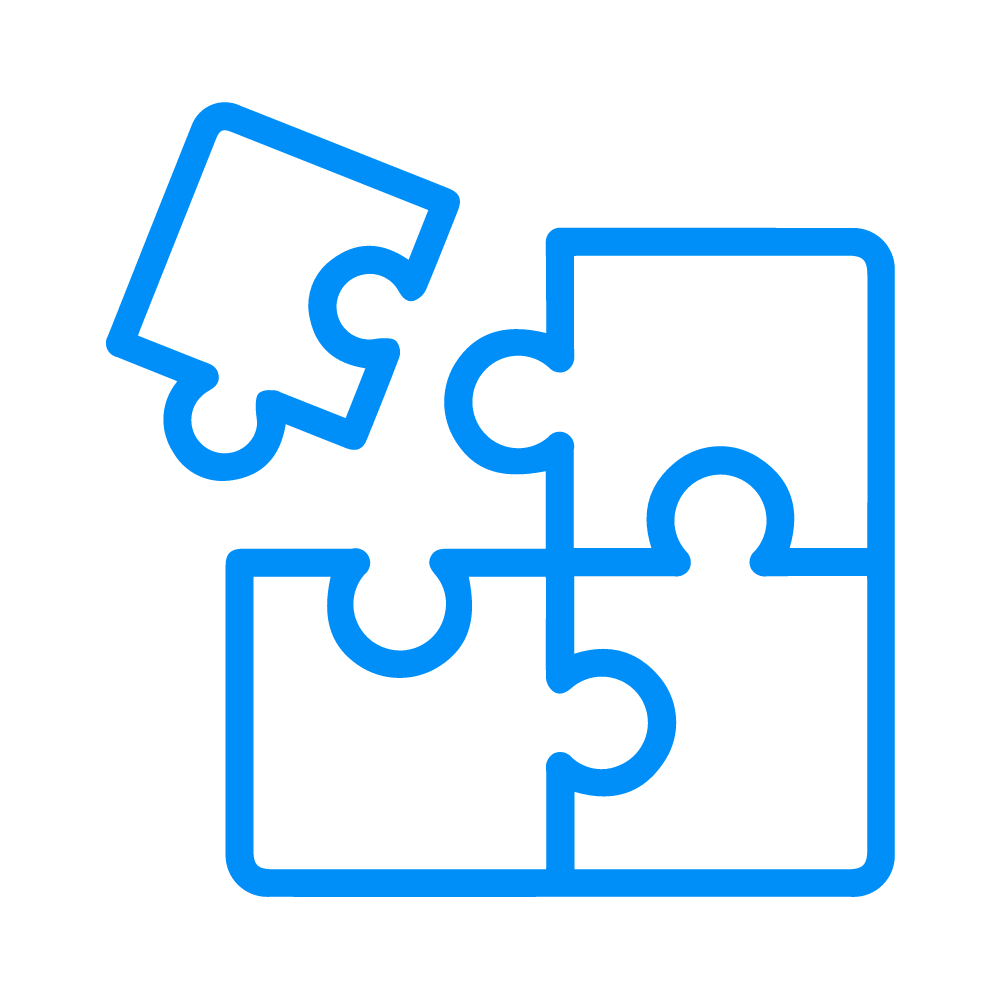
Customization
Mengibar’s Pump Cappers can be tailored to specific requirements, allowing for customized solutions that fit the unique needs of each client.
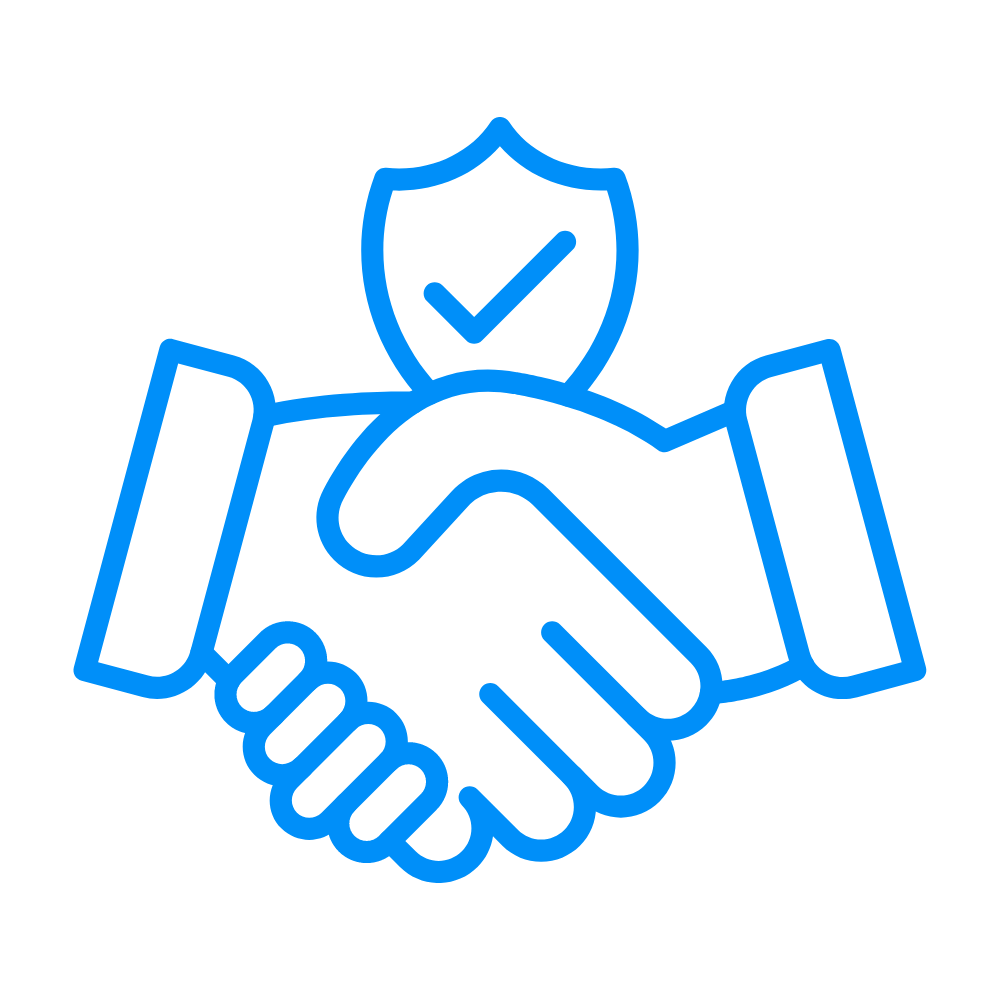
Reliability
Built with robust materials and cutting-edge technology, our cappers provide durability and precision